Drones for Non-Destructive Testing of Industrial Infrastructure
By haadshaikh
In early 2023, a Pakistani firm demonstrated services for NDT inspections to inspect a storage tank utilizing commercial equipment with a UT probe.
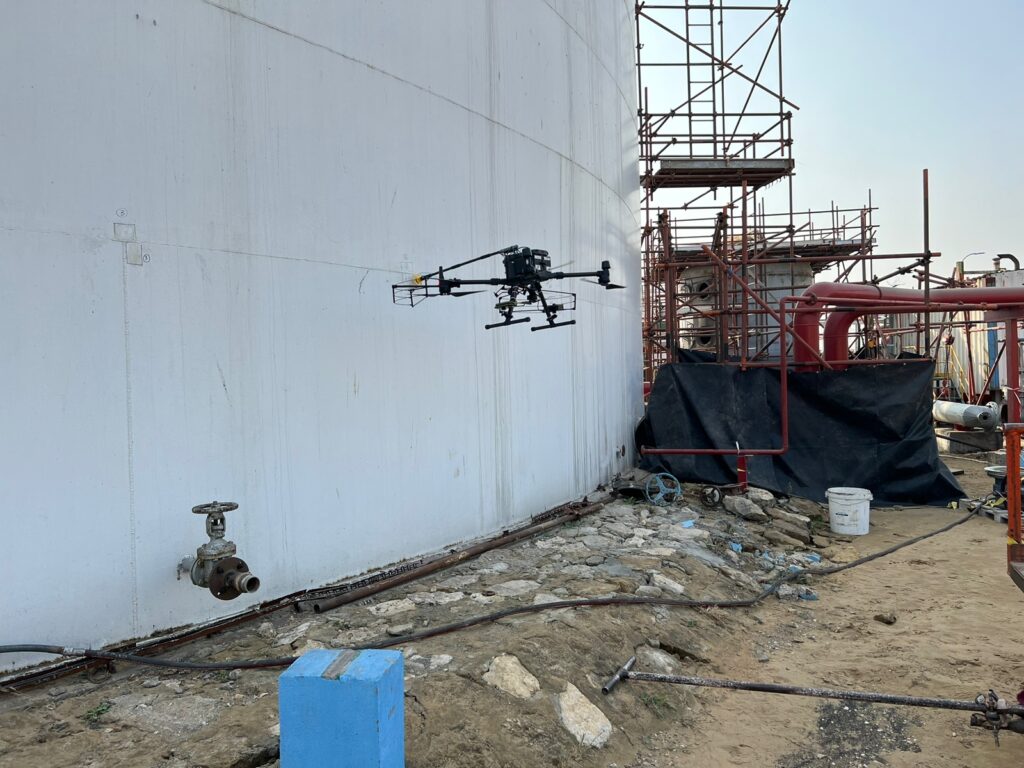
What is Non-Destructive Testing?
NDT (short for Non-Destructive Testing) refers to an inspection procedure that allows one to gather information about a material or structure without causing any harm to it.
Non-Destructive Testing (NDT) is used to gather information about a substance without causing it to be altered (i.e., without destroying it). In this blog, we will focus on one type of NDT which is Ultrasonic (UT) NDT now being used for commercial applications with Drones.
The main distinction between NDT and DT is that NDT does not require inspectors to harm the material being tested, whereas DT does. For example, in Destructive Testing, a piece of the material may be scraped, removed for analysis or modified in a different way on-site (i.e., Macro sectioning, Tensile testing, 3 point bend testing).
Why choose NDT methods?
The importance of non-destructive testing in ensuring that assets are properly maintained cannot be overstated. Here are the top reasons why NDT is utilized by so many businesses around the world:
- Savings: The most obvious answer to this issue is that non-destructive testing (NDT) is more desirable than destructive testing because it allows the material or object being inspected to survive the inspection unscathed, saving precious resources.
- Safety: NDT is especially intriguing because, with the exception of radiographic testing, practically all NDT techniques are safe for humans.
- Efficiency: NDT methods enable a complete and relatively quick examination of assets, which can be critical for assuring project site safety and performance.
- Accuracy: NDT methods have been demonstrated to be accurate and predictable, which are both desirable attributes in maintenance processes designed to ensure worker safety and equipment longevity.
Where is NDT used?
Depending on how broadly you define NDT, you could argue it’s employed in practically every industry on the planet, because visual inspections (whether formalized or casual) occur in almost every workplace in some form or another. Having said that, several sectors require NDT and have structured methods for its utilization.
The industries that require NDT with UT include:
- Oil & Gas
- Power Generation
- Chemicals
- Mining
- Aerospace
- Automotive
- Maritime
Inspectors in all of these businesses utilize three different methods to get access to difficult-to-reach or high-rise locations:
- Scaffolding: Scaffolding necessitates inspectors working at height in order to obtain inspection data.
- Rope access: Inspectors must also work at heights while using rope access to obtain inspection data.
- Drones: Drones can be used by inspectors to collect inspection data remotely allowing them to remain safely outside of tight places or below high-risk locations.
Using drones for NDT
Drones fitted with cameras have been another instrument extensively employed in NDT for obtaining visual data in recent years. Due to technological restrictions, drones could only give supplementary visual data for inspectors for some time, but could not replace inspectors physically gathering visual data themselves. However, as drone technology has advanced, inspectors have been able to use drones as
RVI (Remote Visual Inspection) tools more and more, completely removing the requirement for them to collect visual data manually in some cases.
1. Safety
Drones help improve workplace safety by eliminating the need for inspectors to enter unsafe confined locations to obtain visual data.
Using a drone to capture visual data on assets such as power lines or towers minimizes the amount of time a human needs to physically be in the air on the tower or line. For indoor inspections of assets such as pressure vessels or boilers, employing a drone to collect visual data eliminates the need for the inspector to enter a tight place, thereby reducing risk exposure.
Nondestructive inspections are a safe and effective method of finding flaws that could lead to dangerous situations, malfunctions, or catastrophic failure. They reduce the number of mishaps that occur during testing operations as workers attempt to access difficult-to-reach regions and hostile settings. Furthermore, it reduces the potential of fires and other hazards occurring during traditional destructive testing, such as welding or the use of open flames.
Identifying flaws in advance allows maintenance staff to remedy problems before they occur. This effectively eliminates failure, which could result in fires and accidents to workers and those nearby the impacted institution.
2. Reduced Downtime
Drones can help businesses improve their ROI (Return on Investment) in both indoor and outdoor environments. Nondestructive testing using drones makes it simple, quick, and economical to identify flaws and defects in materials. This allows the maintenance personnel to do quick repairs and replacements before problems arise. Each of the technologies serves a unique function in decreasing the costs and time required to complete a specific inspection. Furthermore, testing without shutting down operations saves the organization time and prevents production losses.
Only a few people, if any, are required to go out into the field to do the inspections. Furthermore, drone-based NDT inspections eliminate the requirement for huge transport vehicles and helicopters to reach inaccessible places. The technologies decrease transportation and insurance costs, and because the tests take less time, the corporation
spends less on lodging and allowances.
Drone-based NDT inspections can swiftly identify the majority of flaws and provide enough information to maintenance employees to allow them to rectify problems and prevent leaks and pipeline damage.
Since a drone inspection can be mounted rapidly, inspections may be undertaken more frequently, allowing flaws to be identified early and boosting asset longevity. With a single examination, these early discoveries can save businesses hundreds of thousands of dollars.
3. Reliable Inspection Data
The NDT can examine the structures and offer detailed data that would have taken many days using standard access methods by employing a drone to visit inaccessible regions.
Drone-based inspections in the oil and gas industry can give dependable and accurate test data on a wide range of properties. The best part is that the inspection process is usually repeatable and can be extremely valuable in determining the effectiveness of any repairs.
The drones may repeat the same experiments from the same place and angle by using location and other settings. This enables maintenance employees to produce precise results and eliminate errors that would otherwise occur when testing at various sites.
Ultrasonic Drone Inspections
A drone equipped with an ultrasonic thickness gauge can make contact with surfaces for testing to measure metal thickness and ignore paint coatings. One such example of a drone already in the market is the skygauge ultrasonic testing drone.
The Skygauge is a drone-mounted ultrasonic thickness gauge designed for both visual and wall thickness inspection. Instead of putting workers’ safety at risk by putting them on ropes, boom lifts, and scaffolding for industrial inspections, the Skygauge allows personnel to stay on the ground while the drone inspects dangerous areas.
The Skygauge drone’s process is separated into three major categories: site gathering, flight path planning, and post-analysis. Workers must verify that the surroundings around the inspection area are clear before checking the structure in question.
The drone uses a force-sensing probe to apply the precise amount of force required to acquire thickness measurements and maintain surface contact during the scan.
The Skygauge’s design allows for precision flying, force contact, wind resistance, and tilted examinations.
UT Testing with Drones around the Globe
- Apellix does UT measurement with precision flight and advanced sensors.
- Eddyfi Technologies helps pipeline operators inspect assets with many types of drones and measurement tools.
- Gecko Robotics uses UT as one of its many inspection methods.
- Mitras uses robots to do NDT on large structures using robotics, automation, and data.
- Terra Inspectioneering and Skyline Drone use drones to inspect confined and hazardous energy assets with UT, visual, and other inspection methods.
There are many applications where the use of drones are better than using traditional methods for inspection in many ways. As the use of these drones for NDT in industries increase, the resulting advantages are very rewarding. When drones and non-destructive testing are combined, the advantages of drone mobility and flexibility, as well as the non destructive nature of the inspection, are realized. This improves safety, saves costs, and avoids manipulating the materials under test.
Drone-based NDT inspection, when done correctly, can give useful information while keeping structures intact. However, it is necessary to grasp the task at hand as well as the type of information it will seek. It is critical to understand both the capabilities and the constraints. Furthermore, understanding the essential standards and specifications in regard to the test is critical.
Drone NDT is a beneficial financial investment since it reduces safety hazards to the NDT technician and, in some situations, offers access to key regions that an NDT technician may not be able to investigate.